Introdução
Sistemas PIMS (Plant Information Management System) são sistemas de aquisição e armazenamento de dados de plantas industriais. Há décadas as indústrias vêm adotando o uso destes sistemas de forma a manter um histórico do funcionamento da planta industrial.
Entretanto, vimos na indústria mais uso do PIMS para acompanhamento de produção e qualidade de produtos do que para uso em Manutenção Industrial. A implementação prática de tecnologias avançadas de manutenção, como CBM, é relativamente limitada na indústria de manufatura. Acreditamos que existe um gap entre o que é possível fornecer de funcionalidades e o que de fato está sendo usado pelas indústrias.
Para se manterem competitivas, as empresas de manufatura devem aumentar continuamente a eficácia e a eficiência de seus processos de produção. A manutenção é um componente vital para garantir o desempenho confiável e seguro dos equipamentos industriais. Tradicionalmente, a manutenção preventiva tem sido amplamente adotada como uma abordagem para evitar falhas e defeitos. No entanto, essa abordagem tem suas limitações, uma vez que as intervenções de manutenção são realizadas com base em intervalos de tempo fixos, independentemente do real estado de saúde dos equipamentos. Para superar essas limitações, a Manutenção Baseada em Condição (CBM) surgiu como uma estratégia eficaz que utiliza dados de monitoramento em tempo real para tomar decisões de manutenção com base no estado atual dos equipamentos.
O uso de CBM possibilita realizar a tomada de decisão baseada em dados, uma vez que a equipe de manutenção passa a dispor de mais uma ferramenta para tomar as decisões de qual deve ser o foco de atuação da equipe de manutenção naquele momento.
Como o PIMS já possui histórico e capacidade de armazenamento dos dados de chão de fábrica ele se torna um aliado para as empresas que pretendem utilizar CBM para auxiliar na tomada de decisão das equipes de manutenção.
Definição de Manutenção Baseada em Condição (CBM)
Qualquer fabricante de bens duráveis define hoje em dia, logo na fase de projeto, um determinado programa de manutenção. Compete aos utilizadores respeitar estas condições de utilização ou, julgando afastar-se destas reformular aqueles planos de forma a garantir o melhor compromisso entre custos de manutenção e de falhas (Assis, 2014).
Podemos assim nos encontrar em uma situação de sub ou sobremanutenção, conforme o equipamento for utilizado. A primeira situação é normalmente a mais comum. Desta forma depreende-se a importância crescente da manutenção, da gravidade da sua ausência, ou da negligência no seu cumprimento durante o ciclo de vida dos equipamentos (Assis, 2014).
As falhas de manutenção mais comuns, segundo Rui Assis (Assis, 2014) são:
- Ausência de lubrificação ou a sua prática em intervalos de tempo inadequados;
- Remontagens Inadequadas (desalinhamento, por exemplo);
- Negligência ou ignorância no monitoramento dos equipamentos (temperatura, pressões, vibrações, etc.).
A CBM vem com a proposta de monitorar os equipamentos em tempo real para prevenir os erros citados no ítem 3 acima, melhorando o monitoramento dos equipamentos.
As estratégias tradicionais de manutenção, como a manutenção corretiva, não são mais suficientes para atender às necessidades industriais, como reduzir ao máximo as falhas e degradações dos sistemas de fabricação (Rastegari, 2017).
O conceito de manutenção evoluiu nas últimas décadas de uma abordagem corretiva (ações de manutenção após uma falha) para uma abordagem preventiva (ações de manutenção para evitar a falha). Estratégias e conceitos como manutenção baseada em condições (CBM) evoluíram para apoiar esse resultado ideal (Rastegari, 2017).
CBM é um tipo de manutenção popular discutido em seminários e na literatura. A CBM pode ser tratada como um método para reduzir a incerteza das atividades de manutenção e é conduzido de acordo com os requisitos indicados pela condição do equipamento. Na CBM, a saúde do equipamento é monitorado por meio de sua condição de operação, que pode ser medida com base em parâmetros de monitoramento como vibração, temperatura, óleo lubrificante, contaminantes e níveis de ruído (Rosmaini e Kamaruddin, 2012).
A disponibilização de mais recursos computacionais para auxiliar o monitoramento dos equipamentos pode contribuir bastante para uma manutenção mais assertiva dos equipamentos identificando defeitos antes que um equipamento venha a falhar.
Benefícios do Uso de CBM
A CBM nos permite identificar e resolver problemas com antecedência antes que ocorram danos. Em sistemas industriais, qualquer dano pode ter consequências graves. A esse respeito, a CBM é um método muito atraente para uma indústria que opera ativos de alto valor (Shin e Jun, 2015).
A CBM nos dá um aviso prévio de falha iminente e maior precisão na previsão de falha. Assim, pode efetivamente reduzir a falha do produto em comparação com outras abordagens. Do ponto de vista da gestão da segurança do produto, o CBM é útil para os tipos de produtos em que a segurança é considerada importante, pois pode aumentar a segurança detectando problemas com antecedência antes que problemas sérios ocorram, o que leva à melhoria da satisfação do cliente devido à alta garantia de qualidade (Shin e Jun, 2015). Portanto, a CBM é necessário para garantir o gerenciamento da integridade do equipamento, reduzir o custo do ciclo de vida e evitar falhas catastróficas (Rosmaini e Kamaruddin, 2012).
A CBM ajuda a melhorar a confiabilidade e a disponibilidade dos equipamentos, pois as intervenções são realizadas quando necessário, evitando interrupções não planejadas e minimizando o tempo de inatividade.
Ao adotar a CBM, observamos que as atividades são direcionadas especificamente para as necessidades dos equipamentos, evitando negligência ou ignorância no monitoramento dos ativos.
Implementação da CBM
A implementação da CBM requer a coleta contínua de dados relevantes para avaliar o estado dos equipamentos. Isso pode ser feito por meio de sensores, sistemas de monitoramento online ou análise de dados históricos. Estes fatos transformam o PIMS em um sistema bem dimensionado e alinhado aos propósitos de monitoramento dos ativos da planta industrial.
É importante identificar os parâmetros críticos que indicam a saúde dos equipamentos. Para isto o trabalho em conjunto com a equipe de manutenção e principalmente os colaboradores com ampla experiência em manutenção e operação destes equipamentos devem ser ouvidos e seu conhecimento deve ser transferido aos sistemas onde a CBM está sendo desenvolvido.
O aspecto central da CBM é o monitoramento de condições, que pode ser realizado usando várias abordagens e empregando diferentes níveis de tecnologia, conforme apresentado na Figura 1 (Rastegari, 2017). O monitoramento de condições pode ser realizado periodicamente ou continuamente. Normalmente, o monitoramento periódico é realizado em determinados intervalos, como a cada hora ou ao final de cada turno de trabalho, com o auxílio de indicadores portáteis, como instrumentos de medição portáteis, unidades de emissão acústica e canetas vibratórias. O processo de monitoramento da condição também inclui avaliações baseadas nos sentidos humanos (monitoramento subjetivo) para medir ou avaliar as condições do equipamento, como o grau de sujeira e cor anormal (Rosmaini e Kamaruddin, 2012). No monitoramento on-line (ou em tempo real), uma máquina é monitorada continuamente e um alarme de advertência é acionado sempre que um erro é detectado.
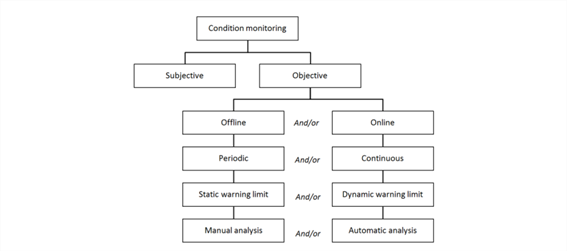
No que se refere à proposta de uso dos sistemas de PIMS presentes na planta industrial, de acordo com o fabricante, várias ferramentas são disponibilizadas para que este monitoramento da saúde do ativo se torne possível.
Citando os dois maiores sistemas de PIMS presentes no mercado brasileiro podemos usar:
- Aveva PI System: pode ser utilizado o PI AF para definição da hierarquia à qual o ativo está inserido, PI Analysis para gerar as notas de saúde de cada ativo e PI Notification para notificar os usuários por e-mail caso tenham equipamentos operando com tendência a falhas. Telas do PI Vision podem ser desenvolvidas com componentes customizados para alertar os operadores do estado de saúde indesejado do equipamento;
- IP.21 da Aspentech: pode ser utilizado o SQLPlus ou AspenCalc para calcular as notas de saúde dos equipamentos e enviar notificações aos usuários. O A1PE pode ser utilizado para gerar a visualização da saúde de cada equipamento da área. Pode-se utilizar também um frontend customizado de acordo com a necessidade dos usuários utilizando o SQLPlus Web Service para trazer os dados do IP.21 para este frontend.
No caso de monitoramento com o auxílio de indicadores portáteis, todos os fabricantes de sistemas de PIMS possuem diversas formas de integração com sistemas externos. Bastando ao analista escolher a melhor forma de entrada dos dados. Já no caso de medições baseadas nos sentidos humanos todos os sistemas de PIMS possuem a opção de entrada manual de dados, sendo assim o analista precisa deixar pronta a opção de entrada manual que melhor se adapte à rotina dos usuários.
Todas estas implementações já foram feitas pela ihm Stefanini a fim de garantir um bom uso dos sistemas de PIMS para CBM.
Casos de Uso do PIMS para CBM
A ihm Stefanini desenvolve sistemas de PIMS para indústrias de diversos segmentos como Mineração, Siderurgia, Papel e Celulose, Saneamento, entre outras. Temos expertise no desenvolvimento de CBM para atendimento às necessidades das equipes de manutenção das plantas industriais.
As abordagens mais recentes de sucesso da ihm se referem ao desenvolvimento de cálculos de saúde dos ativos baseado em:
- Instrumentação dos equipamentos indicando operação fora de limites especificados: são definidos limites muito baixo, baixo, alto e muito alto para a operação dos equipamentos e ao atingir estes limites são dados alarmes onde a criticidade mostrada será de acordo com o valor violado;
- Tempo em que o equipamento ficou funcionando fora do limite aceitável: a nota de saúde do equipamento é calculada de acordo com o tempo de funcionamento dentro de limites aceitáveis. Caso o equipamento opere dentro de um limite ruim por 50% do tempo a nota que vai de 0 a 10 é calculada como 5, se ele operou 100% do tempo em um limite ruim então a nota de saúde é 0, se ele operou 100% do tempo dentro de limites aceitáveis então a nota é 10 e assim as notas vão sendo calculadas em tempo real.
A Figura 2 mostra um exemplo de tela desenvolvida no PIMS para acompanhamento de uma área de secagem. Para cada válvula é feito um cálculo de saúde em tempo real que define se seu funcionamento está normal ou se tende a alerta ou crítico.

Ao clicar em uma das válvulas é exibida a tela da Figura 3 mostrando detalhes da válvula e todas as medições que são usadas no cálculo da saúde. Nesta tela o usuário tem uma visão em tempo real do estado de saúde da válvula.

Outro projeto desenvolvido pela ihm Stefanini integrou um painel de notas de saúde de equipamentos diretamente ao SAP, fazendo abertura automática de notas de inspeção para equipamentos com notas de saúde abaixo de 5. Assim a equipe de manutenção já é notificada para fazer a inspeção nos equipamentos que estão com tendência a defeitos de acordo com as medições realizadas pelos sensores presentes no equipamento. O painel apresenta um treemap onde mostra a nota de saúde, cor de acordo com a nota e o tamanho do quadrado do treemap representa o peso desta regra ou equipamento.

Foi desenvolvido um data hub onde os dados do SAP e do PIMS são integrados para gerar análise e possibilidade de desenvolvimento de BI e Analytics para a equipe de manutenção. Esta camada intermediária apresenta os registros de falha de cada equipamento e as ocorrências, para saber em que data aconteceram e a recorrência das mesmas.
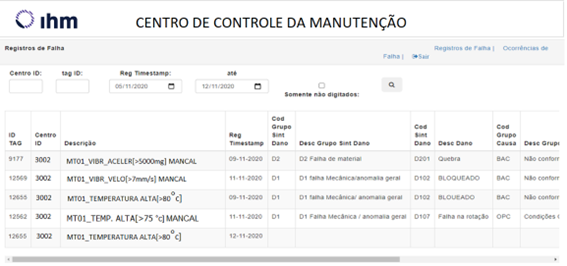
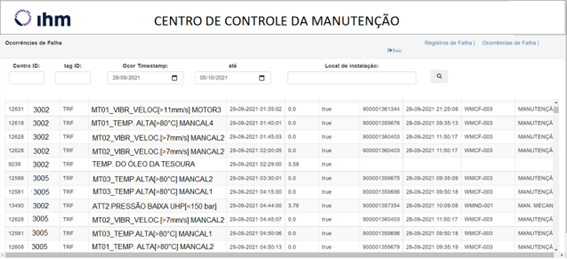
Conclusão
Segundo Rossomani e Kamaruddin 99% das falhas de equipamentos são precedidas por certos sinais, condições ou indicações de que tal falha seria sanada. A disponibilidade e a precisão dos dados (por exemplo, tecnologia baseada em sensores) são alguns dos motivos para oferecer suporte ao CBM (Rosmaini e Kamaruddin, 2012).
Devido à sua ampla utilização em indústrias o PIMS (Plant Information Management System) pode ser um grande aliado ao desenvolvimento de CBM. Em indústrias que já possuem estes sistemas, que vemos no mercado que é a grande maioria, a CBM pode ser implementado com pouco custo adicional e pode trazer grandes retornos para a equipe de Manutenção.
A ihm Stefanini já implementou iniciativas de CBM utilizando PIMS em indústrias de diversos setores e com diferentes sistemas com sucesso.
Os ganhos obtidos com este tipo de sistema dependem do uso dos usuários e disseminação da ferramenta pela empresa para seus funcionários de manutenção. Todos os ganhos citados no capítulo de Benefícios do Uso de CBM são possíveis utilizando as ferramentas oferecidas pelos sistemas de PIMS que existem no mercado.